New pressure blasting cabinet at VULKAN INOX: Investment in the future for more flexibility in surface treatment
Hattingen, May 2025: VULKAN INOX - manufacturer of high-quality stainless steel blasting media - has expanded its machine park with a new pressure blasting cabinet with an integrated quick-change blasting media system. The modern blasting system impresses with its powerful technology, compact construction and robust industrial design - ideal for demanding applications in industrial surface treatment.
Expansion of the blasting technology portfolio with a new pressure blasting cabinet
The newly installed pressure blasting cabinet complements VULKAN INOX's existing machinery and expands the possibilities in industrial surface treatment. Thanks to its versatility and high adaptability, the modular blasting system offers maximum degrees of freedom in the demanding processing of surfaces. It is therefore ideal for sample processing and process development.
In combination with the existing systems for wheel blasting and wet blasting, VULKAN INOX provides its customers with all essential industrial blasting processes - bundled at one location, efficiently and with state-of-the-art technology.
Precise blasting thanks to variable nozzle control
The compressed air blasting cabin enables VULKAN INOX technicians to use both hand-guided nozzle movements and semi-automatic operation with a fixed nozzle arrangement. The blasting nozzle can be flexibly positioned and aligned within the working area. In combination with the precise dosing of the abrasive and the freely selectable working pressure, the effect of the blast can be adjusted precisely and as required. Various nozzle configurations enable precise adjustment and processing of the blast pattern - this ensures optimum processing even with complex geometries and difficult-to-access internal contours.
Flexible adaptation to workpieces and processes
Special product carriers, turntables and rotary baskets enable a wide range of adaptations to the workpieces to be blasted. These ensure optimum alignment, movement and circulation of the workpieces, especially when blasting bulk material. The generously dimensioned side door also allows convenient loading and unloading of the work area, for example using a forklift truck. In combination with a cabin load capacity of 250 kg, this also ensures reliable processing of medium-heavy workpieces.
Quick changeover thanks to quick-change abrasive system
The multitude of applications, requirements and situations in blasting technology require careful selection of the blasting medium. Whether cleaning, roughening, deburring, rounding edges, matting, satin finishing, smoothing or hardening - the abrasive as a processing tool must always achieve the process objectives reproducibly and economically.
In order to be able to develop customer-specific solutions, the pressure blasting cabinet was designed so that almost all types, shapes and sizes of blasting media can be used. A specially designed blast media quick-change system enables the blast media circuit to be emptied quickly and residue-free, so that samples or test series can be produced in quick succession. Even the most demanding workpieces and surfaces can be perfectly finished without long set-up times.
Efficient abrasive recovery for sustainable processes
The heart of the blasting system is the separate Power-Pack with abrasive recovery, blasting pot and filter system, which ensures the sustainable use of high-quality stainless steel abrasives.
During the blasting process, the reusable blasting abrasive and the resulting process residues are extracted from the work area by the recovery system and fed into a high-performance cyclone. This is where precise separation and processing takes place, during which the high-quality abrasive is sifted, cleaned and recovered for the next blasting cycle. Worn abrasive bodies and unwanted residues, on the other hand, are removed from the material cycle and collected by the filter system.
Continuous reprocessing is an essential prerequisite for the sustainable use of blasting media. It enables the economical use of reusable blasting abrasives and ensures their cleanliness and effectiveness over many blasting cycles. The processed abrasive is fed into an intermediate storage silo and automatically feeds the blasting pot below as soon as it is depressurized and opened. The generously dimensioned blasting pot holds up to 150 kg of blasting abrasive, allowing longer blasting sequences to be carried out without interruption.
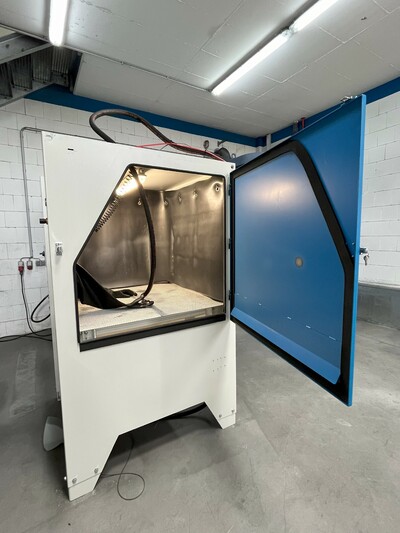
CONCLUSION: Future-proof technology for the highest demands
With the new pressure blast cabinet, VULKAN INOX is once again demonstrating its commitment to quality and customer focus. Andre Hahn, Head of Quality Assurance and Development, describes the latest modernization as a further step towards the future.
“In a dynamic environment, we are subject to constant change with high demands,” he explains. “We meet these challenges both conceptually and by continuously investing in the expansion and modernization of our machinery. The new blasting system increases our ability to react quickly and flexibly to customer requirements and significantly improves our range of services.” Andre Hahn, Head of Quality Assurance and Development
Here you can find further publications of our press release in the trade press: