Sweep blasting or sweeping
Sweep blasting is a special type of abrasive blasting and an effective and established blasting method for gentle cleaning and roughening of sensitive blasting material as well as of demanding substrates. Accordingly, the blast abrasives and process parameters for sweeping must be well matched to the blasting task so that damage to the workpiece by the blasting process can be ruled out.
What is sweep blasting?
Sweeping - also known as sweep blasting or sweep blasting - is a particularly gentle variant of the blasting process. Sensitive surfaces are cleaned in a targeted manner and at the same time slightly roughened without damaging the base material. This method is ideal for demanding substrates such as hot-dip galvanized or coated components, where conventional blasting would be too aggressive.
For the process to work optimally, the blasting media and process parameters must be precisely matched to the respective blasting material. This is the only way to ensure that the surface has the desired adhesion for subsequent coatings - while at the same time protecting it from mechanical damage.
Sweep blast cleaning zinc coatings
Sweep blasting has proved particularly useful in the execution of duplex systems, in which two autonomous protection methods complement each other. They are based on galvanizing and a single-layer or multi-layer wet or powder coating, which together form a corrosion protection system with a very long protection time.
Sweep blasting allows the surface to be prepared effectively and quickly before coating, as the zinc coating is cleaned and roughened in a one-step process.
A primary use of sweeping is to remove adhesion-reducing residues prior to coating application. This includes the inherent impurities of the zinc, such as white rust (zinc hydroxide, zinc oxide and zinc carbonate), but also foreign impurities, such as any passivations that were temporarily applied as corrosion protection.
Favorable surface topography
At the same time, during sweep blasting, the usually smooth surface of the zinc coating is extensively profiled and slightly roughened by the impacting abrasive. The changed surface topography and the resulting enlargement of the total surface area significantly increases the contact area between the zinc and the coating, thus creating more adhesive ground on the same area. The roughness profile created with sweep-blasting also favors mechanical adhesion of the coating and makes it less susceptible to tensile, compressive and peeling stresses.
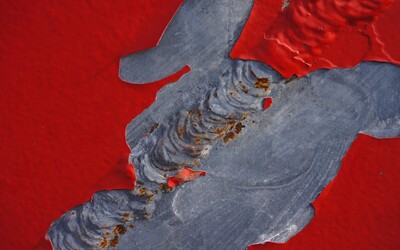
Special case of powder coatings
The surface enlargement by sweep blasting also favors the outgassing of volatile air and hydrogen residues, which are frequently embedded in hot-dip galvanized coatings, especially those with thick layers. This is because the thermo-chemical crosslinking process in powder coatings, which is carried out at high temperatures, favors their escape and can severely disturb the coating structure in the form of bubbles, craters and pores.
The disturbances in the coating structure are not only a decorative problem, but often cause a considerable weakening of the organic protective layer within the duplex system. This is because corrosive media can penetrate through such damaged areas, reach the galvanizing and trigger a corrosion attack. The white rust that forms expands in area and volume, increasingly undermines the coating and consequently leads to loss of adhesion.
Additional annealing after sweep blasting can further support the outgassing process.
Regardless of whether gaseous residues can escape from the zinc substrate present, there is always a risk, even with white rust nests remaining on the surface, that the white rust will decompose into water, CO2 and SO2 during powder coating baking, forming bubbles and causing the coating to lift off. These existing contaminations can be effectively and efficiently removed by sweeping, if the sweep blast cleaning is carried out properly and professionally.
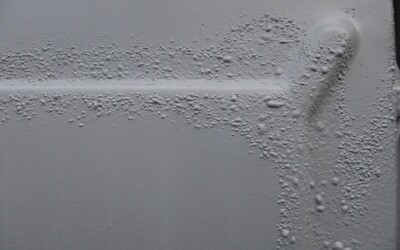
The zinc coating
The zinc coating itself, as an integral part of the duplex protection system, must be intact after sweep blasting and should have as little loss of coating thickness as possible. The precondition for this is first of all a high-quality zinc coating with sufficient layer thickness, where the zinc coating itself has very good adhesive and cohesive properties. If this is not the case, the zinc coating can flake off from the steel substrate even with professional sweep blasting, and edge areas in particular are critical here, or cohesive fractures can occur within the zinc coating.
The loss of zinc due to sweeping must be taken into account when galvanizing, because the protective duration of the zinc coating is primarily determined by its own layer thickness. Thus, the layer thickness of a hot-dip galvanizing before sweeping should be ≥100µ, if the galvanizing material allows it (see DIN EN ISO 1461), so that a minimum thickness of 85µ is still assured after sweep blasting. The measured zinc removal after blasting is at best less than 10µ and must not exceed 15µ under any circumstances.
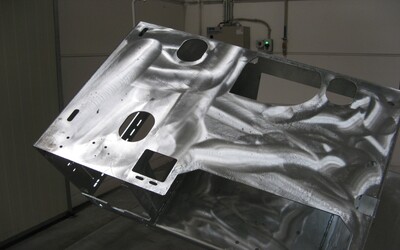
Surface preparation grade
The appearance of the zinc coating after sweep blasting must be homogeneously matt or satin (wheel blast cleaning).
The roughness values, measured with a tactile section gauge, after the sweep blasting process are as follows:
Rz - average roughness depth: 25.0 - 50.0µ
Ra - arithmetical mean value: 4.0 - 6.5µ
RPc - peak number: >40
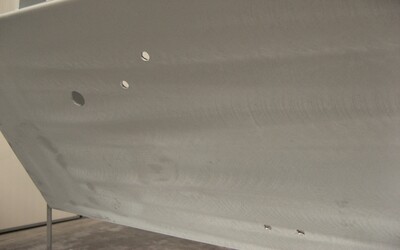
Process execution
For sweep blasting of hot-dip galvanized coatings, the following parameters and blast media have proven effective in practice:
Grain size [mm]
Blasting pressure [bar]
Speed [rpm/min]
Zinc layer
0,10 – 0,50
2,0 – 3,0
-
Uniform matte appearance, zinc removal max. 10-15µ.
0,30 – 0,80
-
1.700 - 2.200
Uniform satin appearance, zinc removal max. 10-15µ.
Strip galvanizing - sendzimir-galvanized
In the case of surface preparation of sendzimir-galvanized steel sheet with a low layer thickness (5-40µ), the extent to which sweep blasting can represent a suitable preparation method must be examined on a case-by-case basis. In any case, the sweep blast cleaning parameters must be even more carefully matched to the material to be blasted. The basic suitability and the required process parameters can be determined and specified in blasting tests.
Surface preparation of stainless steel
Soft sweep blasting is also well suited for cleaning thin-walled and mostly very smooth stainless steel sheet and at the same time preparing it for coating or bonding. Sweeping the surface here achieves greatly improved conditions by temporarily removing the natural oxidic protective layer of the stainless steel and increasing its surface area. Particularly critical substrates, such as weld seams, can also be treated very effectively by the sweep blast process.
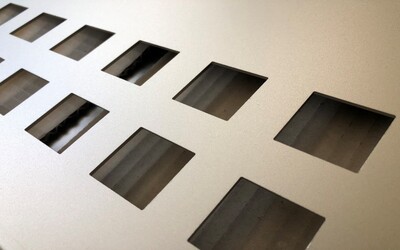
General
As already mentioned, sweep blasting is an effective and efficient as well as safe preparation method, provided that sweeping is carried out properly and professionally. This is because sweep blasting is initially based on the same operating principles as are familiar from conventional blasting processes. However, in many cases, the adoption of familiar blasting parameters would cause irreversible damage to the blasting material or substrate. These include, for example, deformation of the workpiece, material detachment and chipping in the case of sensitive substrates, or roughness values that are too high and make further processing impossible.
Thus, during sweep blasting, the grain energy and thus the beam intensity must be significantly reduced. This is done by reducing the grain mass and/or reducing the grain velocity by using finer abrasives and selecting a lower exit or throw-off velocity.
Applicable blast technology
Sweep blasting can be carried out both in compressed air blast machines and in wheel blast machines. However, there are two process-related restrictions for sweep blasting in wheel blast machines, namely the geometry of the blast material and the choice of blasting medium.
Successful sweep blasting in wheel blast machines requires that the parts to be blasted are of simple design and easily accessible to the abrasive, because the discharge units are fixed in position and allow few adjustment possibilities with regard to the abrasive discharge. In the case of complex part geometries, the desired effect of sweeping can easily be missed if partial areas of the blast material are insufficiently or not at all reached by the blast wheel jet.
When selecting blasting media, it should be noted that mineral blasting media (corundum, garnet, broken glass or slag) cannot be used in blast wheel blasting systems at the present state of the art. This circumstance must be taken into account if high surface outputs or quantities are to be sweep blasted economically and ecologically. However, sweep blasting using blast wheel technology can be realized very easily with angular stainless steel grit and has already been established for many years.
Sweep blasting in compressed air blasting systems, on the other hand, is not subject to any technical restrictions. Due to the manual guidance of the blasting nozzle, the process is highly variable and thus easily adaptable for the user. All recommended abrasives can be used for sweep blasting, but stainless steel abrasive offers great economic and ecological advantages due to its exceptional lifetime.
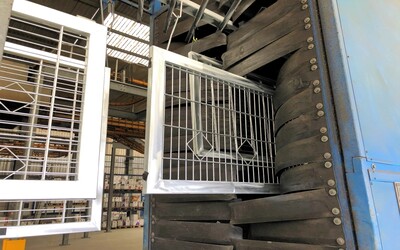